Origin Composites specialises in the supply of thermoplastic composite sandwich panels custom made for our customers' use in a variety of applications including the transportation, marine, leisure and construction industries.
Thermoplastic composite sandwich panels provide a cost-effective alternative to plywood or metal sheets and we can provide a product suited specifically to your company's needs.
We are the sole UK distributor for Compoform who are based in The Netherlands.
Half the weight and twice the strength*
Origin Composites can supply individual sandwich panels 3.2m wide (useable 2.8m) with lengths up to 75m, ideal for single panel, seamless applications such as side walls and roofs of enclosed trucks or caravans and trailers. Thicknesses from between 1cm to 15cm using either foam or honeycomb core material determined by the required performance.
Contact Origin Composites today for a sales visit, a demonstration or technical proposal.
*Compared to plywood
Manufacture
Composite materials are defined as a product made up of several components parts or elements to make a single product.
The composite product offered by Origin is a thermoplastic composite (TMC) sandwich panel.
The inner core material of the sandwich is typically a thermoplastic honeycomb sheet which undergoes a continuous heating and compression process to permanently bond thermoplastic outer layers or skins to both sides of the core material to produce a robust yet versatile single product.
This manufacturing process is undertaken by an in-house developed double belt-press machine which advantageously can produce finished panels up to 2.8m wide with lengths as much as 75m and up to 15cm thick!
The core material and outer layers can be varied to provide a uniquely blended product matched to your specific application.
Features
By virtue of their construction TMC sandwich panels are immensely strong yet light and still display a degree of ductility.
A high degree of mechanical integrity means they are resistant to dents, dings, chips, cracking, splintering or fraying.
Strength to weight ratios are significantly better than traditional alternatives such as plywood or sheet metal.
The inner core and outer layers can be varied by material selection and dimensions to produce the desired mechanical properties specific to your needs.
The outer layers can also be selected to provide desirable visual properties such as gloss finishes, fire-proofing, printed or blank
Alternatively, if properties such as chemical resistance or coarseness for improved grip are more important then these options are also possible.
Direct Advantages
- Highly robust
- Impact resistant
- Easy maintenance and repair
- Rot proof
- Weather and UV resistant
- Reduced weight
- Vastly improved strength to weight ratios
- Panel properties can be customised to the application
Secondary Advantages
- Weight reduction for transportation provides increased payload and improved fuel efficiency through fewer journeys
- Extended service life
- Safer, easier manual handling vs. traditional materials such as plywood or metal sheets
- Faster construction methods
- Manufacturing dimensional capability provides seamless solutions
Benefits
- Reduced fuel costs
- Reduced maintenance cost
- Lower man hours (£) needed in manufacturing
- Longer product life
- Increased carrying capacity
- Reduced total cost of ownership
- HIGHER PROFITABILITY
Eco Credentials
- ISO accreditation
- TÜV Certified
- TMC sandwich panels are fully recyclable
Applications
The applications for TMC sandwich panels are many and varied, and, most are probably still to be identified and developed.
The following are a selection of existing industrial applications:
- Truck sides, floors and roofs
- Panel and Box vans
- Refrigerated trailers
- Traditional trailers
- Caravans and motorhomes
- Horse transportation
- Marine leisure
- Ships
- Accommodation
- Boardings
- Scaffolding boards
- Walkways
- Crates
- Facades
Example application
Comfodeck ® PP-honeycomb floor panel
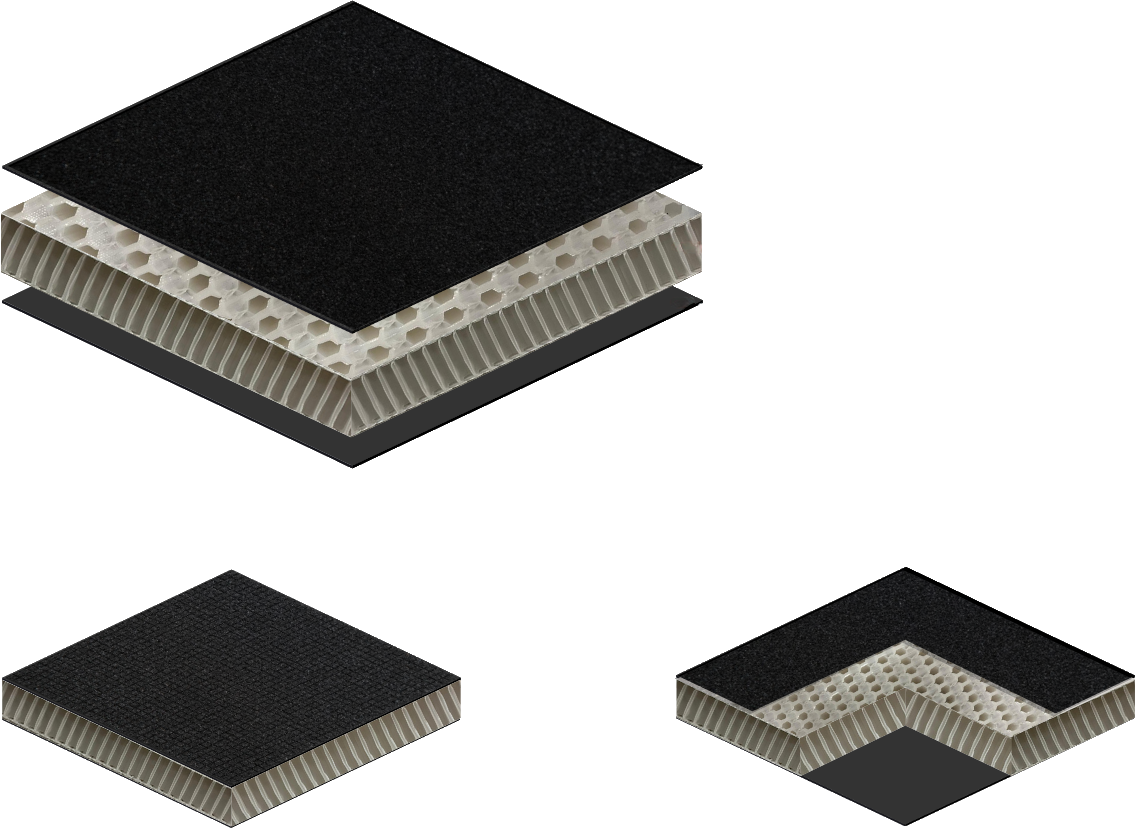
Comfodeck ® PP-foam wall panel
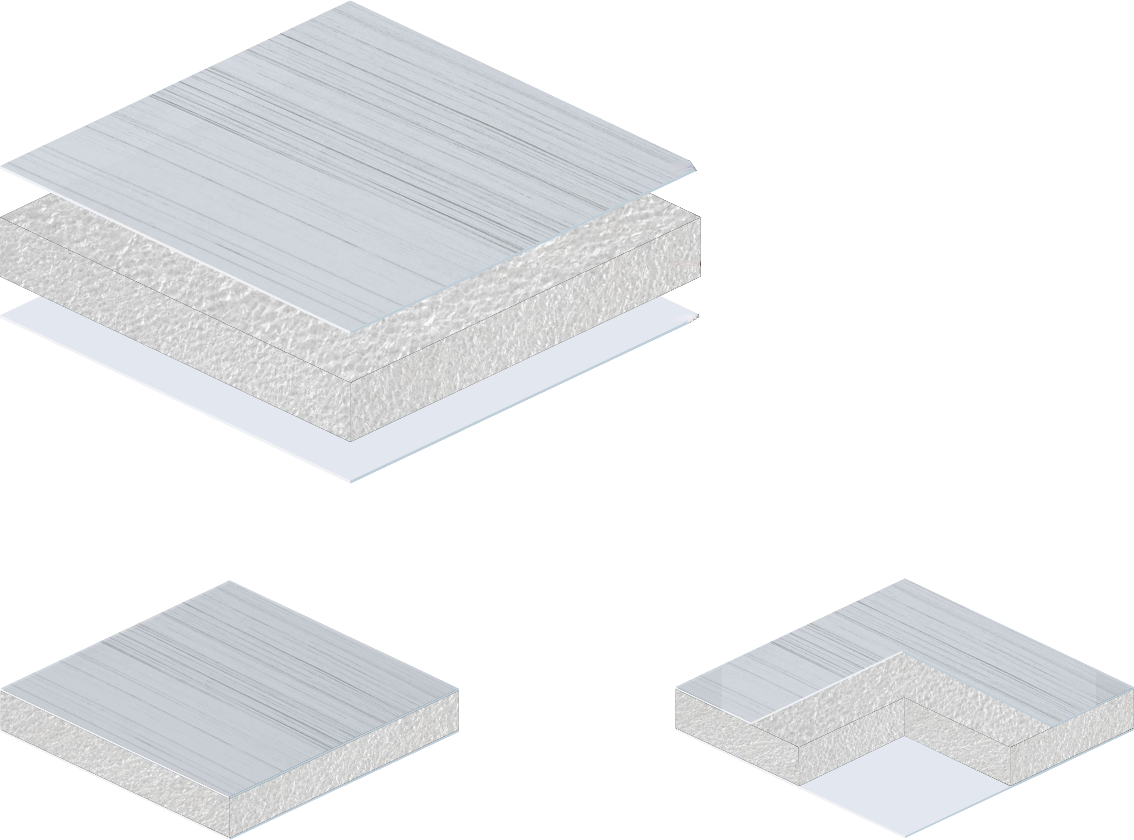
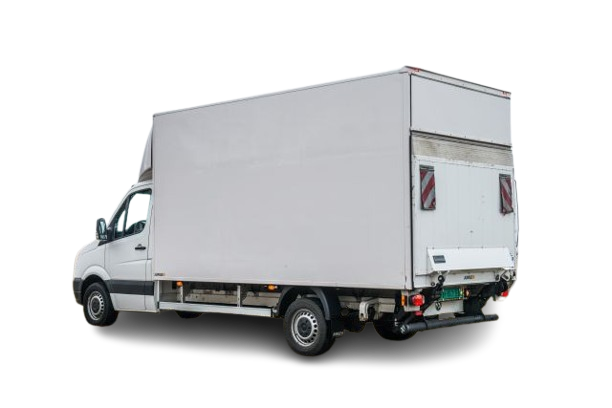
Consider this
One of the most advanced feats of engineering excellence in the 21st Century is the Formula 1 racing car which is now almost exclusively manufactured from composite materials, should you be considering upgrading your manufacturing applications to include composites?
Trees are a diminishing commodity that are needed to produce the oxygen we breathe.
Contact Us
Ian (Micky) McDonald
+44 (0)7473 304557
sales@origincomposites.com
Micky is responsible for technical sales and is based in Central Scotland.
Registered Office
BarleywoodEastertown
Oldmeldrum
Inverurie
AB51 0HB